We developed an £85 million mixed-use student accommodation scheme for Urbanest city, transforming a historic site into one of the most exciting student housing projects in London
The development encompasses a multi-storey student accommodation building spanning across 14 floors facing Vine Street. It also compromises the following elements:
- A six-storey student accommodation building adjacent to Crosswall
- A 12-storey student accommodation building that front onto Crutched Friars
- A 12-storey office building situated to the north on India Street
Beneath the building footprint is a two-level basement that occupies the entire site. The basement accommodates incubator office space, bin stores, bike stores, plant, a café and an exhibition space for The Museum of London’s historic Roman Wall remains.
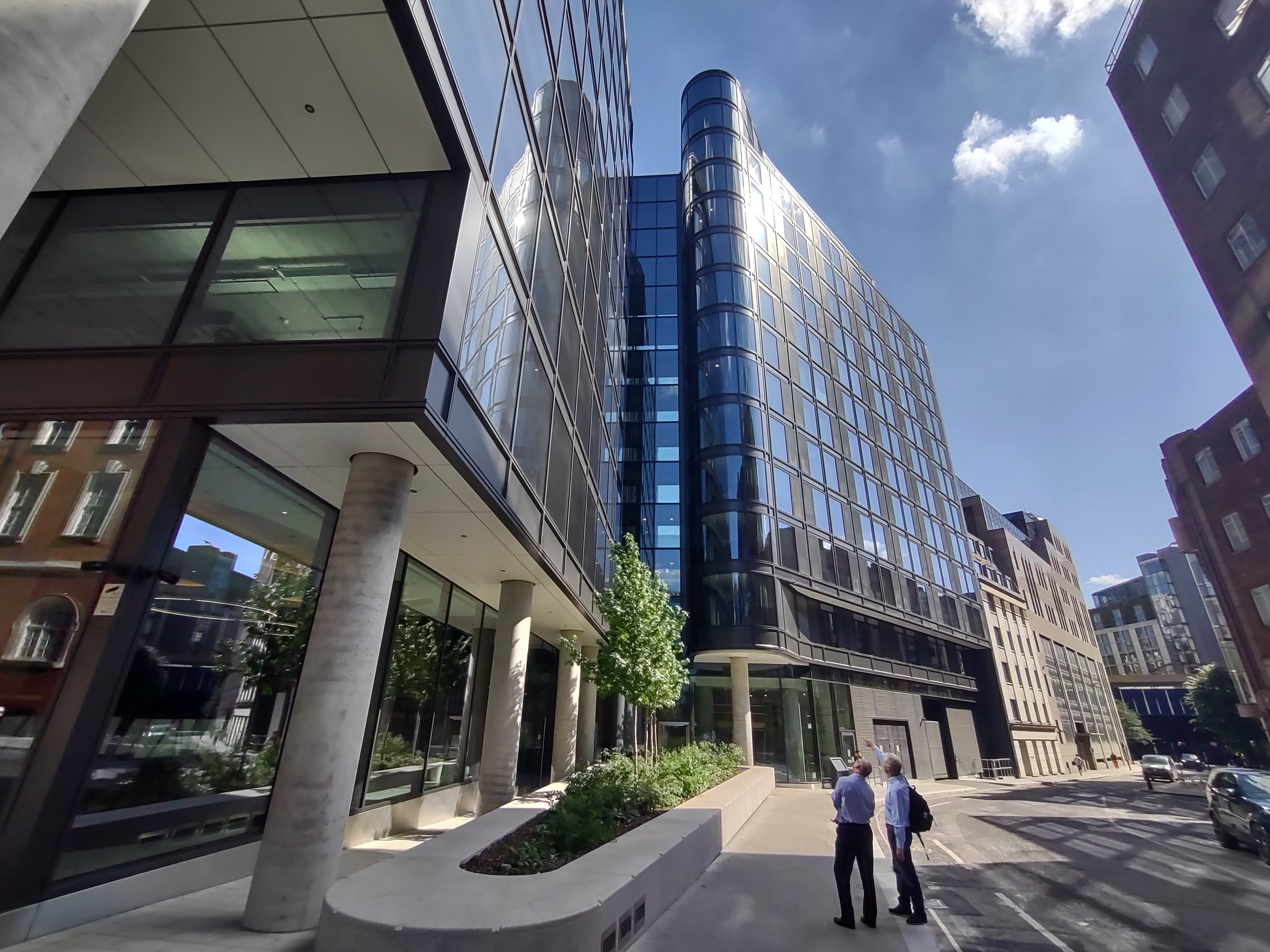
Designing student accommodation, from vision to success
As Urbanest’s preferred construction partner, we were involved from the beginning of the design phase of this student accommodation development. Through early contractor involvement, we were able to optimise the design and costs, comply with regulations and minimise rework and delays. By facilitating effective communication among all project stakeholders, we are able to deliver the customer's vision successfully
project
successful project delivered for Urbanest
MMC bathrooms designed
Benefits of modern methods of construction
Modular and prefabricated construction methods were employed to expedite the project timeline. Student accommodation floors feature 504 bathrooms, meticulously designed as prefabricated pods to optimise room layouts and promote design standardisation. Other advantages of using modern methods of construction include:
- Improved sustainable outcomes. By adopting off-site fabrication, the project significantly reduced waste generation and enhanced the utilisation of recycled materials, thereby decreasing the overall embodied carbon.
- Cost-effectiveness. A strong emphasis was placed on streamlining the pod design to minimise variations within the scheme. This approach had a substantial impact on the cost per pod, resulting in a cost-effective solution. In the end, the project successfully achieved six distinct pod types with minor variations based on fire safety requirements.
- Accelerated construction programme. The pods were lifted into place via large goods hoist and cantidecks to aid the logistical challenges around tight tower crane hook time. This led to a reduction in manhours required during the fit-out stages.
- High-standard of quality. Off-site mock-up was used to inspect quality with the client and sign-off, ahead of completion of pods and deliveries. By leveraging MMC, the project achieved accelerated construction timelines, enhanced sustainability, and cost savings through optimised design and manufacturing processes.
Sustainable living and eco-friendly architecture
The building's façade design incorporates solar shading, reducing cooling loads and improving occupant comfort. As part of the build, blinds are provided in all tenanted spaces, further enhancing energy efficiency. By including planted roof areas, biodiversity was enhanced and rainwater runoff was minimised. In addition, a solar photovoltaic system was installed to convert solar energy into electricity on the roof, facilitating renewable energy generation.
With extensive cycling facilities, including parking and a shared cycle maintenance station, the building supports and encourages sustainable transportation options. By embracing sustainability initiatives, we showcase responsible construction practices contributing to a greener and more sustainable urban environment.
Empowering communities and beyond
Throughout the project, our team actively engaged in numerous community initiatives and events. A pivotal aspect of our commitment to social value was the establishment of a strong partnership with Aldgate Primary School. By collaborating closely with the school, we provided them with valuable support in various impactful ways, including:
- Donating materials and providing lifting plant and operatives to create two covered seating and learning areas in the school's existing roof garden.
- Installed 5 tonnes of sand twice for the nursery’s sand play area.
- Repaired and replastered a retaining wall.
- Conducted informative sessions on construction, materials, and safety for children.
- Converted pupil's artwork into large, laminated posters and displayed them on the site hoarding as part of the school's rebranding.