Our Zero Carbon Construction Site Diary
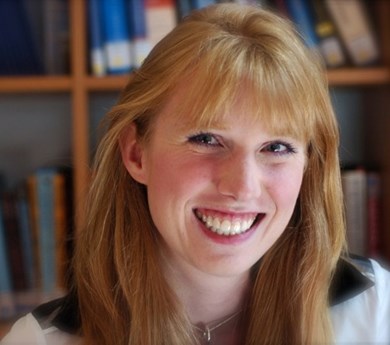
Our all-electric on site experiment
This was the first time on a live Balfour Beatty site that we have used all-electric plant - and with c.75% of equipment on construction sites still diesel-powered, trialling new equipment which reduces emissions and particulates output will be key for the transition to Net-Zero. The key equipment we have needed so far has been a telehandler (fork lift); a two and a half tonne excavator, a two tonne dumper and a wacker, or compaction plate 500mm. We made the decision to go all-electric at the same time for all of these for this six-week period of the project.
Charging and working time
Most battery-powered plant is smaller than diesel plant, and offers enough power for around four-to-six hours of work before it needs recharging. One key observation we made here was that the suppliers didn’t provide information on the capacity at which the various machines could charge. The machines are not provided with charging stations and our suppliers do not manufacture or hire out specific chargers for the plant. We utilised a standard 110v site connection point as this is the cable that was provided with the plant but realistically, a rapid charging connection, similar to what is available for cars, would be necessary if we were using this plant on a larger site. This meant that it was very slow to charge them, and we largely did it overnight. If these were being used on a larger site, we would need to have robust charging infrastructure in place, meaning that sites would essentially have to be redesigned to allow for effective - and low carbon - charging infrastructure. When setting up our sites, mains connections can sometimes be a barrier as there is insufficient capacity available within the local gird. This challenge will become more substantial as electric plant does develop and therefore net zero construction sites may therefore need to look at onsite energy generation to allow charging of the plant. This would lead to a much larger temporary site set up, both in terms of land take, lead in times and materials.
When we set up a site, our rule of thumb is to allow for 100 amps for cabins, and another 100 amp for everything else, although we use our Power Profiler tool to ensure that use of the most cost and carbon efficient site compound set up. Although the amount needed for cabins is going down as we increasingly use our eco cabins, if we were charging all of our large plant from the same supply, we would need to add up to another 100 amp, which would require early conversations with the supplier.
Furthermore, if all of the plant were plugged in at the same time, over lunchtime for example, there would be an electricity surge, so a charging schedule would need to be planned into the overall programme of works.
Telehandler
For the telehandler, working at full capacity, we got maximum four hours per day - which is only really half a day’s work. Even though we had the largest EV model available, it had a
maximum six metres vertical lift, which is less than the larger, diesel models we tend to use - increasing the planning burden. On a bigger site, with more plant, this would have added more complexity to our detailed planning.
Excavator
The small excavator didn’t have as much power for digging as the diesel version either, with a capacity of around four or five hours of hard digging. Once we understood how it worked, we scheduled the day accordingly, including an hour-long charge mid-work. This isn’t how we usually operate, and having to manage these stretches of time was part of the learning curve. This is the first two and a half tonne excavator our supplier has and the first that we’ve used, so we’re feeding back to our supplier so others have more information when they use the same kit.
Dumper
The dumper was no problem and we didn’t have to change anything in terms of how we usually work. We got a full eight hours of work from it and were really impressed with it.
Compaction plate or wacker
The wacker was a lot quieter than a standard diesel wacker, with far less vibration. Our operators also found it easier, though slightly heavier, and really liked it. Our supplier provided two batteries with the wacker, so if one ran out, we were able to change it over and have one on charge, which allowed us to maximise productivity.
Cost
As with electric cars and vans, electric plant is far more expensive than diesel, however, reduced fuel costs and maintenance requirements can make it cost-effective in the long run, which is particularly relevant given current high fuel costs. The upfront cost is also likely to come down over the long-term as it enters mainstream use. Each charge was significantly cheaper than filling up a diesel alternative – a real benefit given the huge increases in fuel costs seen in the past year, not to mention the carbon reduction.
However, if the machines aren’t able to work to the same capacity as diesel plant, it impacts on programme and on cost, which makes them less viable at scale for larger sites. The larger plant isn’t yet available in electric-powered form.
Health and safety and usability
One of the main advantages of electric over diesel plant was that they produce zero emissions. This not only is a clear step in the right direction for the construction sector, it also means that they can operate in enclosed spaces or on smaller sites without additional ventilation and carbon monoxide monitoring. We noticed a clear difference in terms of the air quality and the noise – to the point where we would be concerned if using them at scale - particularly for the telehandler and the dumper. While they make a noise reversing, they
are so quiet during standard operations, our operating procedures and safety training would need updating to make sure we keep our workforce safe, or a noise would need to be added to ensure people know they are there - bearing in mind that people often hear before they look.
Operators found the machines very user-friendly and liked using them. Familiarisation training was limited due to the plant being new, which meant that operatives had to familiarise themselves in a safe area of the site. The conclusion was that there is not a great deal of difference between operating the diesel and electric versions, however, Balfour Beatty will want to update safety and training procedures, change the plant specifications for electric, and amend our checklists to ensure we have safe operation and charging procedures in place.
We also need additional steps to be put in place to ensure that the plant is ready to use : operatives are used to making the machine safe, locking the cab and leaving, but would now also have to remember to plug it in.
Is electric the future?
In spite of the benefits, all-electric plant isn’t yet a realistic option for our bigger sites, or for heavy plant. Just as the range on electric cars isn’t there yet, so the length of time plant can operate flat-out is an issue for the construction sector. Elsewhere in the business, we are buying large amounts of piling machinery. It’s very difficult to make electrification work for big pieces, especially without a mains grid connection – and we need to ensure that there is capacity in the network. The range when they are not plugged in is limited. These larger pieces of electric equipment can also be twice the price of standard plant, and customers are often not prepared to pay the increased hire charges for them. Our view is that, for heavy plant, the priority for the industry has to be to accelerate the energy transition to hydrogen rather than relying on electric to provide the solution.
We are leading on work to make combustion engines work with hydrogen fuel through our partnership with JCB and Sunbelt Rentals, which we hope will be ready within the next 18 months for plant such as telehandlers, traditional digger sizes – big, but not massive kit. We are also working with GeoPura and Siemens Energy on hydrogen fuel cells to generate power without an electrical connection. The potential of this work is huge. Replacing the diesel generators that power our site mobilisations and compounds with hydrogen would see a significant reduction to our carbon footprint, given that 46% of our sites sampled use diesel generators to power temporary accommodation units on site. This is industry-leading, but very expensive work - which makes business cases less viable. Our intention therefore is to work towards setting a cost per tonne of carbon, so we aren’t only looking at headline costs and value, but are being responsible by valuing the costs in terms of carbon savings as well.
We are also working on other, complementary technologies, for example, thin film solar panels on top of our temporary accommodation set ups on our construction sites. If we roll this out across all our modular accommodation on sites, combined with hydrogen generators, we would not only reduce our carbon emissions, we could also save between £3 and £5 million a year in costs. Replicated across the sector, this could be a game-changer.
There is much to do before these become viable solutions. Critically, there is not yet enough green hydrogen being produced, and there remain challenges in terms of the infrastructure for transporting hydrogen around the country. This means that it will be 2025 at the earliest before these become fully viable solutions at any scale.
However, using smaller and medium sized electric plant is definitely something we will continue to pursue, taking each scheme on a case-by-case basis and using a mix-and-match approach that, in general, electric is less useful for larger plant that needs to be used constantly, for eight hours, rather than intermittently. We are already rolling out battery-powered small and medium-sized plant across our business including drills, breakers and wacker plates. Our experience is that the maintenance of these pieces is far lower . Manufacturers are also collaborating to make the batteries for small and medium plant interchangeable, which makes it more realistic to own some of this plant.
Decarbonising the plant used on construction sites is an area that is moving quickly, with options including digital, automation and remote-controlled kit which improves safety by removing the people-plant interface, increasingly coming to the fore alongside electric plant and emerging hydrogen. We have a number of robotic innovations in use across the business, including Boston Dynamics’ ‘Spot the dog’ providing 3D laser scans, and the use of remote control wacker plates in our Rail and Highways businesses. Alongside the use of telematics to reduce energy use, this is an area where we expect to make significant progress in the next three to five years.
Key learning |
Our action |
Standard Operating Procedures will need to be updated to account for the different operational rules for sustainable plant. |
Plant checklists and guidance documents are having alternative fuels sections added and new inspection processes are being developed. |
New equipment will have new safety requirements - we cannot assume that the safe site of the future will require the same approach as safety does now. |
These safety requirements are being captured. Internal plant specifications are being amended to cover safety requirements. |
The journey to Net-Zero requires us to embrace new technology (such as EV plant) - but it shouldn’t mean chasing inefficient solutions when other sustainable will become available in the longer term. |
We will take each site on a case-by-case basis and always seek the most efficient plant, using our Fuel Hierarchy as our guide.
We will also continue to invest in our work on hydrogen as our view is that this is likely to be where the future lies for heavy plant. |
The broader change from to EV and beyond will require us to reconfigure our supply chains and planning assumptions to cope with different capacities and efficiencies of machinery. |
This is being passed on to all relevant colleagues to ensure that the learnings are understood and help to drive progress. |
If you have observations or queries on the points outlined in this entry, please contact: Veena.Hudson@balfourbeatty.com.