Our Zero Carbon Construction Site Diary
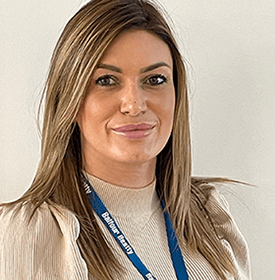
Construction Consolidation Centre
Although the site at the Royal Botanic Gardens is big, the working area itself is quite tight, allowing little space for deliveries or materials storage. Having considered the options, we’ve concluded that using a Construction Consolidation Centre (CCC) within a few miles of the site is the best way of ensuring the timely delivery of goods for to site in a sustainable way. The fundamental function of a CCC is to receive and breakdown large consignments from various supply chains, hold in short-term storage and deliver consolidated loads to site according to the daily resource requirements of collective building trades.. Our intention is to try and select a zero carbon transport method from the distribution centre to our site.
The benefits of this approach include:
- Replacing larger polluting vehicles with smaller, lower carbon options for the last stage of the journey of materials to site. This will mean fewer pollutants being released into the local environment around our project location.
- We are able to buy in bulk, hopefully, allowing the Client to benefit from bulk-buy discounts.
- Removal of excess packaging at the distribution centre rather than at site. This is important as in the distribution centre the packaging is kept relatively clean and dry, maximising the chance of the packaging being reused or recycled. Onsite, large amounts of our materials are exposed to the elements as they are stored prior to use. Packaging will still be required to comply with safety requirements for handling and distribution round site but pallets for example would be returned to the consolidation centre rather than being held onsite.
- Just in time deliveries meaning less material has to be stored onsite which reduces waste generated via materials being damaged or ruined due to weather exposure onsite. Less energy will also be used for onsite storage and distribution around site as the materials can be distributed directly to the place of use.
This isn’t something we’ve done before in Scotland, so we are taking best practice examples from where this is more commonly used, particularly around London. The aim is to choose a facility that also gives us the space to look at using modern methods of construction (MMC) which offer potential to keep carbon emissions lower. This CCC would then act as a sort of logistic and distribution centre for the scheme.
As we’re looking at the options, we’re considering the following points:
- It must be delivered at no additional cost to the customer.
- We need a location that’s as close to the site as possible, so we aren’t generating unnecessary emissions in getting the goods there – and it needs good main road access.
- The sustainability of the facilities, for example, how are the buildings being powered – we ideally want them to be powered using renewables, to keep emissions low.
- How will goods and materials be delivered to the distribution centre: are there any sustainable transport options? Bringing materials by train unfortunately isn’t an option as there aren’t any near enough connections, but what are the next best options?
- How the vehicles delivering materials from the distribution centre to site will be fuelled.
- Rather than simply hiring an empty warehouse, can we work with one of our key supply chain partners, using one of their facilities? The aim would be to add benefit to them while removing the need for them to make additional journeys delivering goods from their facility to our warehouse. We would also be looking to drive down the carbon footprint of our materials by working collaboratively with a supply chain partner in this way, engaging them early and sharing our materials list to encourage them to interrogate their own supply chain to find the lowest carbon options.
- How much space is available, as we are keen to maximise the potential of using MMC options.
- Although the scheme itself is scheduled to take seven years, we have currently only been appointed to work on the scheme for just over two years. We therefore need the distribution centre to be available for a minimum of that period, but also to possibly be available for the full seven years.
We’re actively looking at five options and will be making a final decision in the next few weeks. However, it’s taken us several months to get to this point which means that we are missing opportunities to include this in subcontract enquiries which are being issued to the supply chain currently, to ensure they engage with our successful partner. So, a key learning we’ll be taking forward is that if this distribution centre model works for us, the customer and our supply chain partner, we need to make these decisions more quickly to reap the full benefit.
Sustainable workwear
Safety is absolutely paramount to everything Balfour Beatty does. That means that we buy large amounts of Personal Protective Equipment (PPE) to protect our workforce from health and safety risks.
As we interrogate every element of what we do on this scheme, we’re also looking at the PPE we use. We want to make sure it’s as sustainable as possible, so we’re exploring different options. Our guiding principle and top priority as we do so, is that there can be no compromise on safety.
Our hard hats are already made using recycled content. However, we’re also now trialling on this scheme sustainable PPE including hi-vis jackets and vests made from recycled bottles; safety glasses with 100% recycled nylon frames made from fishing nets - recycled and still 100% compliant to international safety standards. The Traffi Glove range we procure are already certified as Carbon Neutral. This means that at no extra cost, the safety gloves we use have zero negative impact on the environment.
We’re also trialling a new recycling programme onsite. This will mean that, rather than going to in the bin, to landfill, when it’s broken or worn out, all PPE will be recycled and used either to make new clothes or fuel. We’ll receive a report every quarter confirming the quantity of products that’s been recycled into clothing and what percentage has been turned in to pellets for energy. This could make a huge difference, extrapolated over the whole business.
We’ll be assessing the new PPE and taking feedback from those using and wearing it, and I’ll be passing on the learnings to our supplier and to the rest of the Procurement Team. They will then hopefully be used as Standard/Core Products, if there is no compromise on current standards of PPE. We already have other projects due to kick off in 2022 that are keen to have the results of the trial so they can replicate this more sustainable approach.
Measuring our carbon emissions
One of the things we’ve been wrestling with on this scheme is how to measure and benchmark our emissions and set meaningful targets to reduce them. Our own approach on this scheme is to try to drive down the carbon emissions associated with every element, but the formal metrics need to be defined in agreement with the customer.
This project was conceived and designed with BIM level 2 and Balfour Beatty uses an Excel based internet tool to assess energy use and embodied carbon. For projects that are designed with BIM Level 3 Balfour Beatty can utilise its own cutting-edge carbon tool, the AutoBIM Carbon Calculator, which automatically links Building Information Modelling (BIM) data to embodied carbon data from the Inventory of Carbon and Energy (ICE) database.
Establishing what the true baseline is and what is being included in the definition of embodied carbon is something we are working closely with the customer on, but which hasn’t yet been finalised, partly because we’re engaging at a very early stage in what will be a seven-year long project. It’s also a really complex area. There are a number of different options in terms of which guidance the scheme could follow and all of these define and measure embodied carbon, or scope 3 emissions, slightly differently.
From our perspective as contractors working on hundreds of different schemes across the UK, it would be helpful if there were a single definition. This would allow us to more effectively benchmark our own schemes and to begin measurement from the outset. This is why we’ve been working closely with the Scottish Futures Trust on our Fife College pathfinder project for the Net Zero Standard for Public Buildings. This standard tries to set out a more consistent approach in terms of plotting a route to Net Zero and what should be monitored and reported on at each stage. The standard draws together, builds on and signpost existing standards rather than creating another standard which is really important – we don’t need new standards, we need consistency. The whole supply chain requires this clarity to make everyone efficient.
Key learning |
Our action |
We’ll be assessing the effectiveness of the CCC model, the impact on carbon emissions and the benefits delivered for our customer and our supply chain partner, but our hypothesis is that this could offer significant benefits |
We will document the benefits the distribution centre model brings and will share the findings internally |
To be able to gain the full benefit of the CCC model, we need to be able to include the details in subcontract enquiries issued to the supply chain currently, to ensure they engage with our successful partner. |
Decisions need to be made more quickly to reap the full benefit. |
Using a PPE recycling scheme has the potential to save tonnes of waste from going to landfill if extrapolated over the whole business. |
Once the trial has concluded, the results will be shared with the rest of the business to ensure as many schemes as possible benefit. |
There are more sustainable PPE options available. |
We’ll be assessing the new PPE and taking feedback from those using and wearing it. Learnings will then be shared with our supplier and the Procurement Team. They will then hopefully be used as Standard/Core Products, if there is no compromise on current standards of PPE. |
We need to work collaboratively with our customers and designers to ensure that as we transition to digital tools, that information generated from day one of the design process is compatible with the desired modelling and management tools for construction and operation. |
This is a journey we have already started – trying to define minimum digital standards from the onset of a project to ensure that all parties gain the benefit of a truly digital collaborative experience. We will continue to work with customers and to disseminate learnings across our business. |
Defining what the net zero aspirations for a project are, and what will be included in the carbon footprint reporting, right at the concept stage of a project is so important. |
We will continue to work collaboratively with our customers and continue to push for early engagement at the concept stage of new projects. |
If you have observations or queries on the points outlined in this entry, please contact: Veena.Hudson@balfourbeatty.com.