Our roadmap towards a zero carbon construction site
As part of our Connect Roads M77/Glasgow Southern Orbital project, we’ve retrofitted three vehicles with hydrogen hybrid technology and established Scotland’s first construction hydrogen hub.
Working collaboratively with ULEMCo, Logan Energy and PlusZero Power, we have successfully retrofitted two salt spreader HGVs and one Impact Protection Vehicle (IPV) with hydrogen hybrid technology demonstrating the viability of reducing carbon emissions in heavy construction plant and equipment.
Following the retrofit, the two salt spreader HGVs have reduced their carbon emissions by around 26% with the IPV also reducing its emissions, albeit at a slightly lower rate. We have also set up a green hydrogen supply, on-site storage and refuelling infrastructure for the hybrid vehicles and we’re now analysing our road test data to identify further improvements.
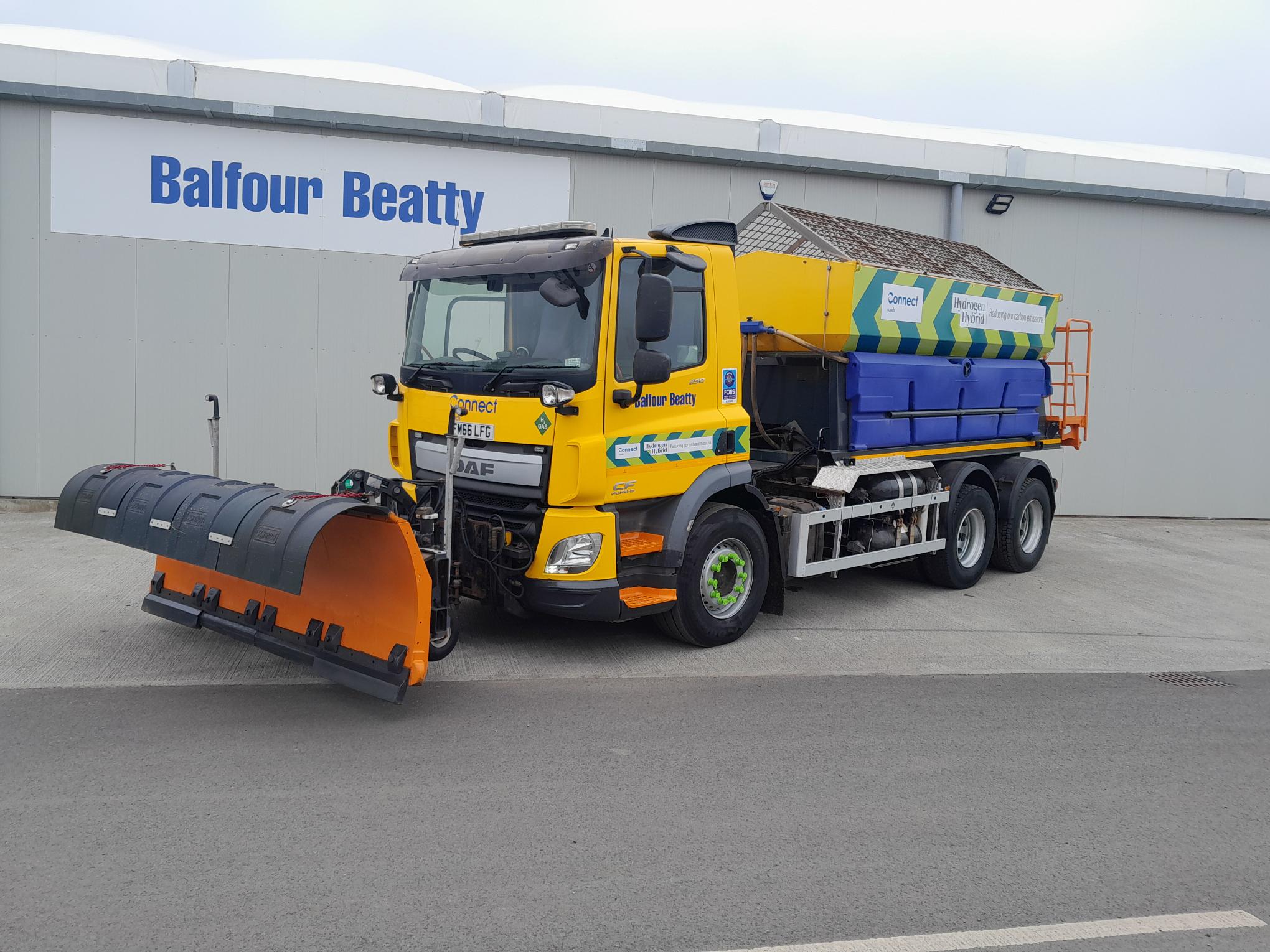
In an aim to share best practice across the industry, we will regularly share updates on the success of the M77 hydrogen retrofit trials as well as any barriers we’ve faced and the solutions we have developed.
Key learnings, August 2024
Retrofit is fast, straightforward and reduces emissions
Whilst retrofitting existing vehicles with hydrogen hybrid technology may not be the ultimate solution for decarbonising heavy plant and equipment, it is an effective, fast, and straightforward technology that is available today. It delivers a substantial reduction in tailpipe carbon emissions, as seen during our road trials, making it a valuable interim measure as we work towards our carbon reduction targets with other benefits including:
- The equipment can operate in diesel-only mode, reducing the risks associated with hydrogen availability and new technology adoption.
- The hydrogen system is automatic, requiring only familiarisation training for drivers, with no changes in vehicle operation except for during refuelling.
- The vehicles will run in hydrogen mode when the engine reaches its optimum running temperature and when engine regeneration is not happening, meaning the technology has the potential to be used across a wide variety of plant and equipment. However, it is less useful for vehicles used intermittently where the engine does not stay at an optimum temperature for extended periods.
- Retrofitting is an effective way to gradually build demand for hydrogen. This allows for the supporting hydrogen infrastructure, such as supply and refuelling technology, to grow to the necessary capacity that will be needed and avoids a sudden need for large volumes of hydrogen that the market may not be ready to supply.
Safety first
The refuelling process is new for our operatives and requires careful attention and an understanding of hydrogen gas as the refuelling area is classified as an ATEX zone, a designated area where there is a risk of explosion due to the presence of flammable gases, vapours, or dust.
To mitigate the risks associated with refuelling the hydrogen hybrid vehicles, our operatives have been provided with antistatic clothing to prevent static electricity from igniting the hydrogen gas. We have also partnered with Hydrasun, a leading international provider of integrated fluid transfer, power and control solutions, who specialise in handling high-pressure gasses to provide comprehensive hydrogen gas training to ensure our teams can follow the required safety protocols.
Supply is key
The supply of hydrogen gas is currently a barrier to a wider roll out of hydrogen retrofits without funding. However, the hydrogen supply landscape in Scotland is expected to improve significantly from 2026 onwards, as various government and private investment projects come to fruition and start providing green hydrogen in much larger quantities.
Transporting hydrogen is also a significant challenge and the transient nature of the construction industry does not fit the current hydrogen rollout model, where investors and suppliers seek guaranteed consumers (known as off-takers) within the local area via dedicated pipework. We are working with suppliers to address this and ensure they understand the importance of mobile hydrogen deliveries to our construction sites.
Our green hydrogen power supply is currently provided by PlusZero Power supplies via the Aberdeen City Hydrogen Energy Storage (ACHES) facility operated by Aberdeen City Council. However, we lack a backup supply if this facility requires maintenance or repair.
Mobile refuelling is essential
At the start of our hydrogen journey, we primarily relied on permanent fuel stations or offsite refuelling at suppliers’ facilities. While these options are suitable for HGVs delivering goods across the country, the preferred refuelling model for construction plant and equipment is on-site refuelling as:
- Some plant cannot operate on public highways.
- Offsite refuelling causes costly downtime.
- For projects maintaining public highways, onsite refuelling ensures access to fuel in extreme weather to keep roads open and safe.
Mobile hydrogen supplies are vital for the construction industry and we have been actively focussing our efforts on working within our supply chain to develop a mobile refuelling model that can be set up on temporary sites. We considered a number of refueller units including the Logan Energy refueller, the Hydrasun mobile refueller and the Nanosun Pioneer unit. The suitability of refuellers depends on the end use and likely volumes, with one of our key learnings being that the refuellers can have a significant lead in time. Ultimately, only the Logan refueller was suitable to meet our programme timeframes.
Importance of collaborative working
As part of our journey to be Scotland’s first construction hydrogen hub we collaborated with Aberdeen City Council and First Bus Aberdeen who shared their experiences from establishing the Aberdeen City Hydrogen Energy Storage (ACHES) public hydrogen refuelling station and transitioning to hydrogen-powered buses. Their guidance and sharing of best practice was invaluable as we embarked on our journey.
Other lessons we have learned through collaboration with others include:
- Hydrogen technology is continually evolving and presenting new options. This can make investment decisions challenging, as certainty about the chosen solution and technology is essential.
- Due to the technology’s relative infancy some project information sharing required a non-disclosure agreement. While necessary, entering into this type of agreement requires additional time to be factored into any hydrogen deployment project.
Safe systems of work in the hydrogen industry differ significantly from those in construction. Bridging these two industries required substantial time, patience, and determination from both our team as the customer and our supply chain partners.