A successful trial by Balfour Beatty VINCI of a ground-breaking digital measuring system for concrete has led to a roll-out across multiple HS2 sites, cutting carbon and driving efficiencies on the construction project.
VERIFI® is a pioneering technology that enables real-time monitoring, measurement, and management of fresh concrete properties during transportation.
By utilising on-truck sensors linked to proprietary patented algorithms, VERIFI is the first digital solution to replace manual consistence (e.g. slump) and temperature testing of fresh concrete. In simple terms, this means the concrete truck-mixer tracks itself to the point of delivery, tests itself prior to discharge and auto generates pour records for quality assurance purposes.
Over the last two years, Balfour Beatty VINCI has worked with supply chain partners Saint Gobain Construction Chemicals who developed VERIFI, and their concrete supply partners Tarmac and Aggregate Industries to test and validate the system.
A full-scale site trial involving over 20,000m3 of concrete demonstrated accuracy and confidence in the technology, and HS2 Ltd has now approved the roll-out across further sites.
One of the key benefits of the system is the elimination of concrete waste which would have been produced from manual sampling and testing. When the solution is rolled out across Balfour Beatty VINCI’s section of the route, this could result in cutting 1,500 tonnes of carbon.
Analysing the entire volume in the truck instead of spot samples results in improved quality control and more accurate readings. Safety is also improved due to less plant-person interface and manual handling on site.
In addition, it enhances productivity and efficiency by delivering clear digital readouts, eliminating delays associated with sampling and testing processes, which allows for better scheduling and reduces potential bottlenecks in the construction timeline.
Steve Phipps, Head of Materials Engineering at Balfour Beatty VINCI said: “The initial concept of using this technology to reduce manual testing has been developed into a fully integrated digital monitoring and reporting system between producer and customer.
“It’s very rewarding to have finally implemented this digital solution after a process of trials, validation and approvals, made possible by great teamwork. Now that implementation is underway across our HS2 sites in the Midlands, we will start to see the significant benefits.”
HS2’s Materials and Durability Lead, Jon Knights said: “This is a fantastic example of how HS2, working collaboratively with supply chain partners, can provide the ideal testbed for cutting-edge technologies. As the UK’s largest infrastructure project, it’s a great step forward for HS2 Ltd to formally supplement this digital surveillance technology with manual consistence and temperature testing of fresh concrete to reduce waste and increase safety and productivity.
“We have set big ambitions to drastically cut carbon as we build HS2, and digital surveillance solutions support us on this journey, not only bringing multiple benefits to the project, but paving the way for a new era in the construction industry.”
Frederic Guimbal, EVP at Saint Gobain Construction Chemicals said:“We’re delighted that the adoption of VERIFI represents a significant step forward for the HS2 project, bringing tangible benefits in terms of quality control, productivity, safety, sustainability, planning, reliability, and digitisation.
“This innovative solution demonstrates the power of collaboration and paves the way for the integration of digital methods in future concrete standards across the construction industry.”
Ryan Griffith, HS2 Technical & Quality Manager at Tarmac, said: “The concrete industry is truly modernising. The carbon benefits and transparency from plant to pour are now a reality with the acceptance of VERIFI digital consistency measurements for the concrete we supply for the construction of HS2.
“Having worked closely with Balfour Beatty VINCI and VERIFI on implementing this technology, it is a huge step forward to have a complete digital concrete quality system that is improving outcomes for customers.”
Joseph Hartley, HS2 Technical Manager at Aggregate Industries said: “Working with VERIFI is a monumental step change in supplying quality assured concrete to our customers. The visibility it gives to ourselves and to our clients is unprecedented. The ability to monitor, maintain our product and track vehicle movements allows significant environmental and cost benefits for us and HS’’
“We have been able to work closely to Balfour Beatty VINCI and the VERIFI team to fully understand VERIFI and get the maximum out of the system giving us the opportunity to collaborate with everyone on the project. Having worked in the ready-mixed concrete business for 36 years, VERIFI is one of the most significant upgrades to our operational capability I’ve seen.’’
VERIFI optimises planning and coordination through GPS tracking of vehicles equipped with the technology. This real-time tracking capability improves the management of concrete delivery, enhancing logistical processes on-site.
Importantly, after careful calibration, VERIFI ensures reliable outcomes and compliance by providing accurate measurements for acceptance or rejection of concrete loads, maintaining the same standards as traditional testing methods. This guarantees the structural integrity and compliance of the construction materials used in the HS2 project.
Following the technical reviews of the trial data conducted by Balfour Beatty VINCI, VERIFI, and HS2 technical specialists, HS2 Ltd approved the use of the VERIFI Digital Measuring system as a departure from the existing standards. This approval encompasses the monitoring of all in-situ structural concrete supplied by Tarmac and Aggregate Industries on the West Midlands section of HS2’s Phase One route.
ENDS
All non-media related enquiries should be directed to +44 (0)20 7216 6800 or info@balfourbeatty.com
Notes to editors:
- Balfour Beatty is a leading international infrastructure group with over 25,000 employees driving the delivery of powerful new solutions, shaping thinking, creating skylines and inspiring a new generation of talent to be the change-makers of tomorrow.
- We finance, develop, build, maintain and operate the increasingly complex and critical infrastructure that supports national economies and deliver projects at the heart of local communities.
- Over the last 114 years we have created iconic buildings and infrastructure all over the world. Currently, we are working to deliver Hinkley Point C, the first UK nuclear power station in a generation; constructing the world-class arts and cultural facility, the Lyric Theatre, in Hong Kong; and designing, building, financing, operating and maintaining the Automated People Mover superstructure at the fifth busiest airport in the world, Los Angeles International Airport.
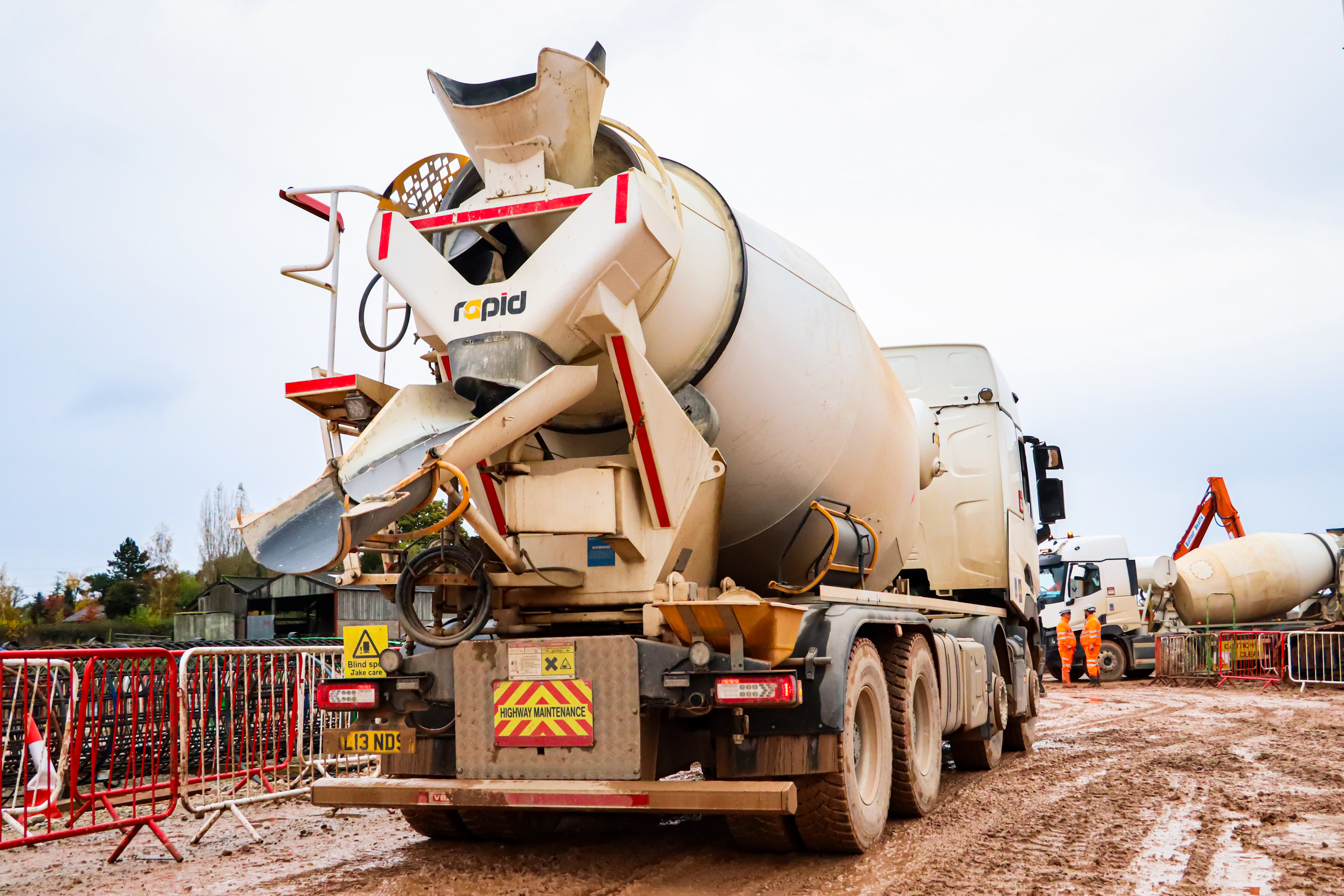
Pioneering technology enables real-time monitoring, measurement, and management of fresh concrete properties during transportation